Our Courses
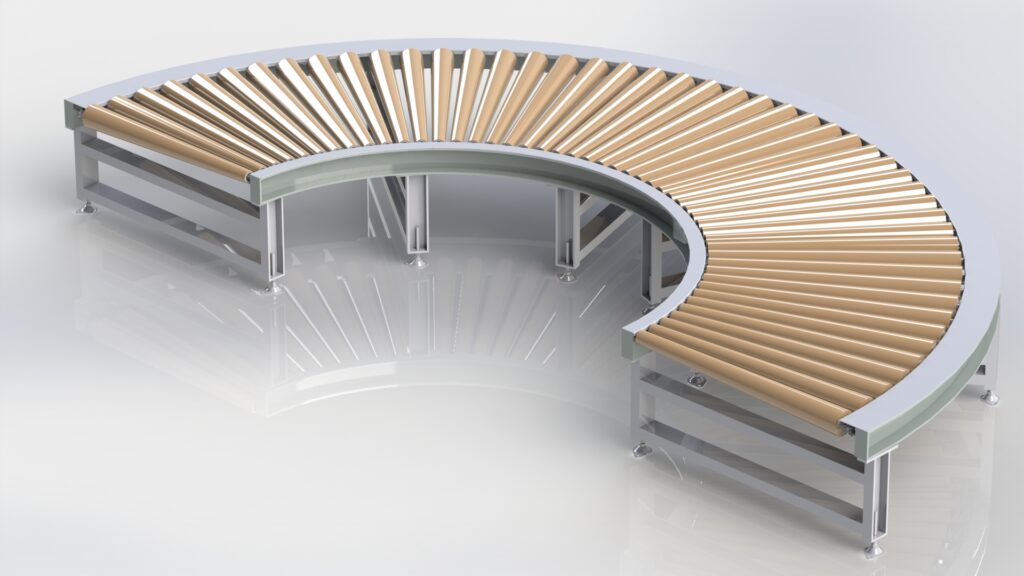
Solidworks Course
What's in this course?
SolidWorks is a powerful CAD (Computer-Aided Design) software used for creating 3D models for many industries like Product Design, Mold & Die Design, Sheet Metal Industries, New concept design, Machine Building & manufacturing, Reverse engineering, detailed drawings and much more. Here is a list of features that you can learn in SolidWorks with us.
Sketching
Draw Tools
- Line: Create straight lines.
- Circle: Draw circles by specifying centre and radius.
- Rectangle: Generate rectangles using corner points.
- Arc: Create arcs by defining centre, start, and end points.
- Slots:
- Spline: Draw complex curves with spline points.
- Polygon: Create multi-sided polygons.
- Ellipse: Draw ellipses by specifying major and minor axes.
- Fillet, Chamfer, Text, Point, Much More…
Modify Tools
- Trim, Extend, Convert, Offset, Mirror
- Linear & Circular Sketch Pattern
- Move, Copy, Rotate, Scale, Stretch.
Dimension
- Smart Dimension, Baseline, Chain, Ordinate, Path Length
Relations / Constraints
- Coincident, Perpendicular, Parallel, Tangent, Horizontal, Vertical, Collinear, Concentric, Equal, Equal Arc Length, Midpoint, Symmetric, Pears, On Surface
Fully Define Sketch, Repair Sketch, Quick Snap, Rapid Sketch, Instant 2D, Shaded Sketch.
Drawing and Detailing
- 2D Drawing: Create detailed 2D drawings from 3D models.
- Annotations: Add dimensions, notes, and symbols.
- Views: Generate various views, such as front, side, isometric, and section views.
- Tables: Insert tables, such as BOM or hole tables.
Advanced Features
- Design Tables: Automate variations of parts and assemblies using Excel.
- Configurations: Create multiple versions of a part/assembly within the same file.
- Macros: Automate repetitive tasks using VBA or other scripting languages.
- Design Library: Save and reuse commonly used features and components.
- Data Migration: Imported Geometry, Import Diagnostics, Check, Recognize Features, etc
Feature Creation
- Extrude: Convert sketches into 3D features by extruding.
- Revolve: Create 3D features by revolving a sketch around an axis.
- Sweep: Create features by sweeping a profile along a path.
- Loft: Generate complex shapes by lofting between multiple profiles.
- Boundary: Generate complex shapes by Boundary between multiple profiles.
- Fillet: Add rounded edges to features.
- Chamfer: Create beveled edges on features.
- Shell: Hollow out a solid model.
- Hole Wizard: Create standard holes, including counterbores and countersinks.
- Pattern: Duplicate features in linear, circular, or other patterns.
- Rib, Draft, Wrap, Intersect, Mirror.
- Reference Geometric, Curves, Instant 3D.
Surface Modelling
- Extruded Surface: Create surfaces by extruding sketches.
- Revolved Surface: Generate surfaces by revolving a sketch around an axis.
- Swept Surface: Create surfaces by sweeping a profile along a path.
- Lofted Surface: Produce surfaces by lofting between multiple profiles.
- Boundary Surface: Produce surfaces by Boundary between multiple profiles.
- Filled Surface: Patches a surface within a boundary defined by edges, sketches, or curves.
- Freeform, Planar, Offset, Ruled Surface
- Surface Flatten, Delete, Replace Face.
- Delete Hole:
- Trim Surface: Trim away parts of a surface.
- Untrim Surface:
- Extend Surface: Extend surfaces to meet other geometry.
- Knit Surface: Combine multiple surfaces into a single surface.
- Thicken, Thickened Cut, Cut With Surface.
Direct Editing
- Move Face: Offset, Translates and Rotates any Faces, Features and bodies
- Move/Copy Bodies: Moves. Copies and Rotates Solid and surface bodies.
- Delete/Keep Body: Deletes or Keeps one or more solid or surface bodies
- Split: Creates multiple bodies from a single body.
- Combine: Combines two or more solid bodies to create a single body or another multibody part.
Assembly Operations
- Insert Components: Add components to an assembly.
- Make Part in assembly
- Mate: Define relationships between components to control movement.
- Move & Rotate Component
- Smart Feature
- Motion & Simulation
- Hole Series
- Exploded View: Create exploded views of assemblies for better visualization.
- Bill of Materials (BOM): Generate a list of components used in an assembly.
Sheet Metal
- Base Flange/Tab: Start a sheet metal part.
- Convert to Sheet Metal:
- Lofted-Bend:
- Miter Flange, Hem, Jog, Sketched Bend, Cross-Break, Swept Flange.
- Edge Flange: Add flanges to edges.
- Bend: Add bends to sheet metal parts.
- Fold/Unfold: Fold or unfold sheet metal parts for better visualization and fabrication.
- Forming Tool:
- Sheet Metal Gusset:
- Tab and Slot.
- Extruded Cut, Simple Hole, Vent.
- Unfold, Fold, Normal Cut.
- No Bends, Rip, Insert Bends.
- Flatten.
Weldments
- Structural Member: Create structural frames using standard profiles.
- Trim/Extend: Adjust members to fit precisely.
- Gusset: Add gussets for strength.
- Weld Bead:
Mold Tools
- Insert Mold Folders: In the Feature Manager creates subfolders for molds in the surface bodies folder.
- Parting Line: Defines parting lines to separate core and cavity surfaces.
- Shut-off Surface: Creates mold shut-off surface by creating a surface patch along a parting line or edges that from a continuous loop.
- Parting Surface: Creates a parting surface that extrudes from parting line or edges and splits the model cavity from the core.
- Tooling Split: Insert a tooling split feature to create the core, cavity and parting surface.
- Core: Extracts geometry from a tooling solid to create a core feature.
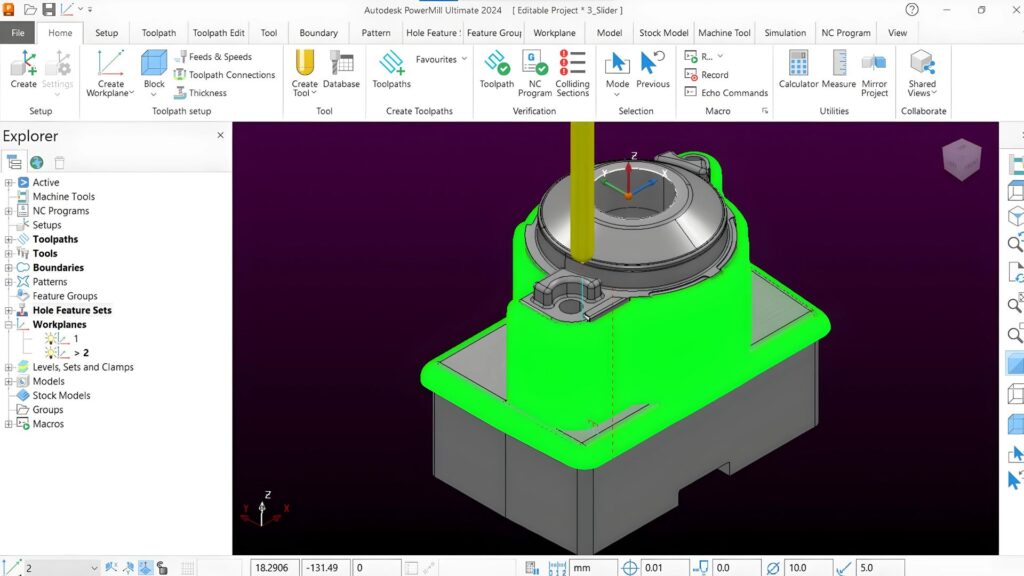
PowerMill Course
What's in this course?
Autodesk PowerMill is a powerful software solution for complex and high-speed machining applications. It offers a wide range of operations to optimize the manufacturing process. Here’s a list of key operations available in Autodesk PowerMill:
1. Roughing Operations:
- Area Clearance: Removes large volumes of material efficiently using various strategies such as offset, raster, and adaptive roughing.
- Rest Roughing: Targets material left from previous roughing operations to ensure efficient material removal.
2. Semi-Finishing Operations:
- Rib Machining: Specialized for removing material from rib-like features in molds and dies.
- Offset Area Clearance: Prepares the part for finishing by following the contour of the surface.
3. Finishing Operations:
- Raster Finishing: Uses parallel passes to produce high-quality surface finishes on complex 3D surfaces.
- 3D Offset Finishing: Follows the shape of the model for consistent surface finish.
- Spiral Finishing: Generates continuous spiral tool paths for smooth surface finishes.
- Flowline Finishing: Follows the natural flow of the surface for a superior finish.
4. High-Speed Machining Operations:
- Trochoidal Milling: Reduces tool wear and enhances efficiency in high-speed cutting conditions.
- Adaptive Clearing: Adapts to material conditions dynamically for optimal cutting performance.
5. Rest Finishing Operations:
- Rest Finishing: Targets residual material left from previous finishing operations for a cleaner finish.
6. Feature-Based Machining:
- Hole Drilling: Automated drilling cycles for different hole types and patterns.
- Feature Recognition: Automatically identifies features such as pockets, slots, and bosses for efficient machining.
7. 5th Axis Machining Operations:
- Swarf Cutting: Utilizes the side of the tool to cut along the surface.
- 3+2 Machining: Locks the tool at a fixed angle for complex 3D cutting.
- Simultaneous 5-Axis Machining: Enables full 5-axis movement for complex geometries.
8. Toolpath Verification and Simulation:
- Toolpath Simulation: Visually verify toolpaths to detect collisions and errors before actual machining.
- Material Removal Simulation: Simulates the material removal process to ensure optimal toolpath strategy.
9. Customization and Automation:
- Scripting and Macros: Automate repetitive tasks and customize workflows using PowerMill’s scripting capabilities.
- Toolpath Templates: Create and reuse toolpath templates for consistent and efficient programming.
10. Optimization and Analysis:
- Toolpath Optimization: Adjust toolpaths for improved efficiency and reduced machining time.
- Feedrate Optimization: Dynamically adjusts feed rates based on cutting conditions to enhance tool life and performance.
11. Collaboration and Data Management:
- NC Program Management: Organize and manage NC programs for efficient workflow.
- Cloud Collaboration: Share and collaborate on projects with team members using cloud services.
By leveraging these operations, users of Autodesk PowerMill can achieve high precision, efficiency, and quality in their manufacturing processes.
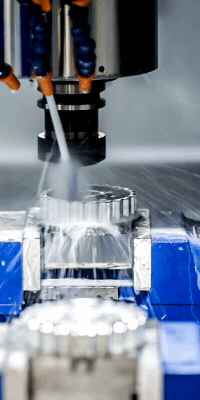
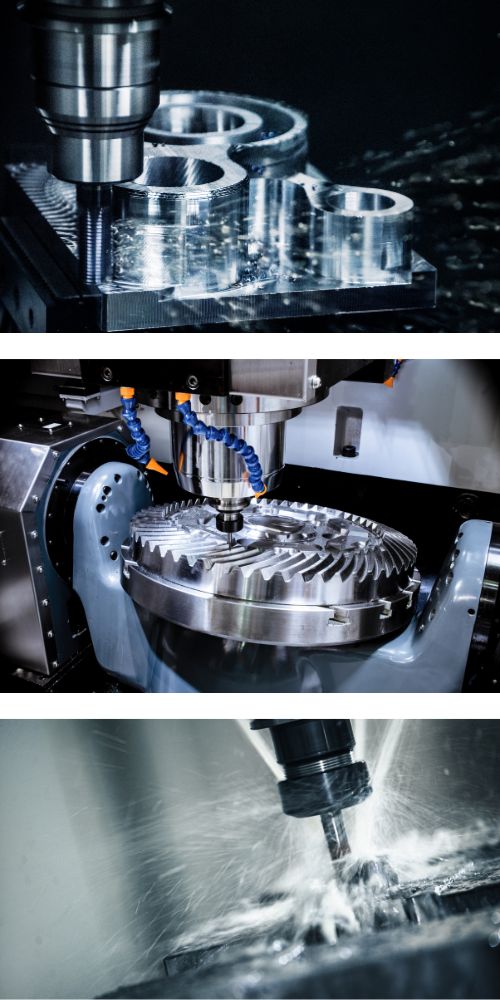
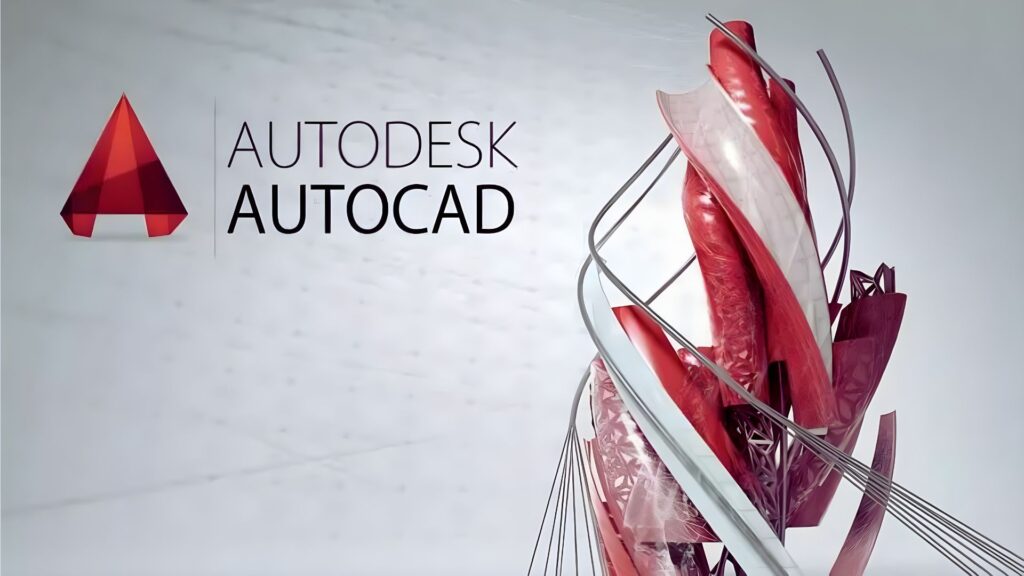
AutoCAD Course
What's in this course?
An AutoCAD course typically covers a range of topics designed to help users master the software for various applications. Here’s a general outline of what an AutoCAD course might include:
1. Introduction to AutoCAD
- Overview of AutoCAD and its interface
- Understanding the workspace and basic commands
- Customizing the workspace
2. Basic Drawing and Editing Tools
- Drawing basic shapes (lines, circles, rectangles, etc.)
- Using editing tools (move, copy, rotate, scale, etc.)
- Creating and editing polylines and splines
3. Advanced Drawing Techniques
- Working with layers
- Drawing precise objects using coordinates
- Creating and using blocks
- Understanding object properties
4. Annotation and Dimensions
- Adding text and annotations
- Creating and modifying dimensions
- Using leaders and multileader.
5. Working with Blocks and Attributes
- Defining and inserting blocks
- Editing blocks
- Using attributes in blocks
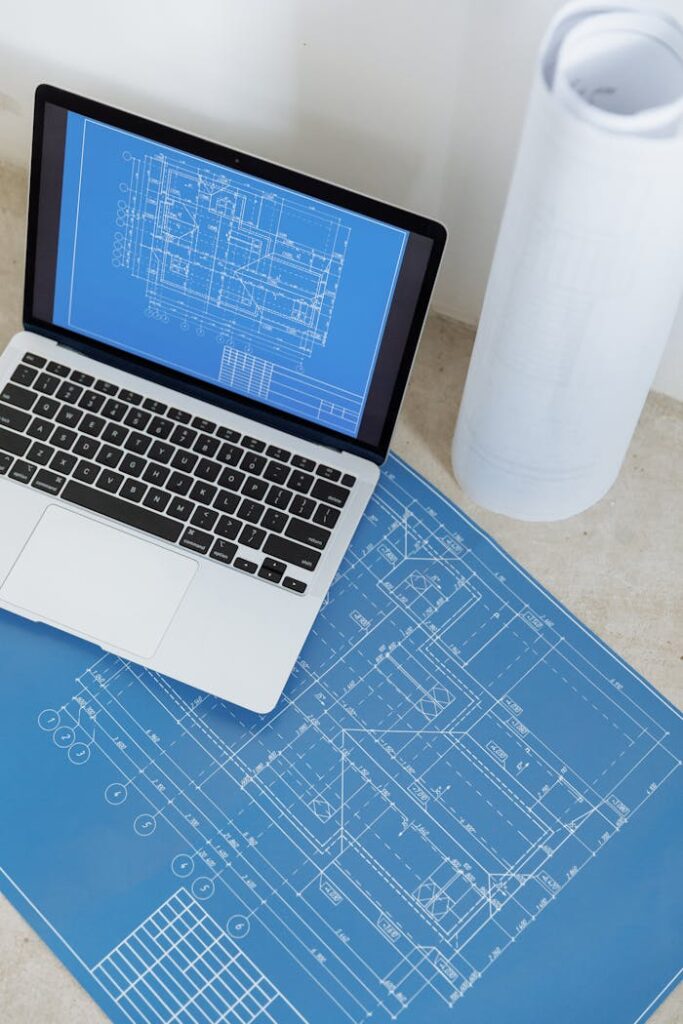
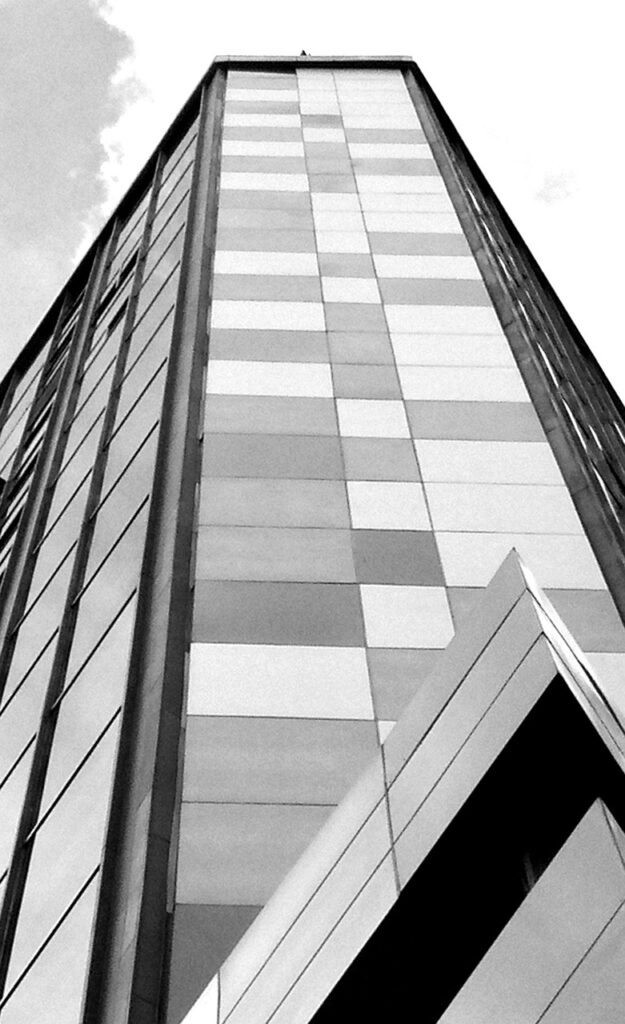
6. Hatching and Gradients
- Applying hatches and fills
- Modifying hatch properties
7. Layouts and Plotting
- Understanding model space and paper space
- Creating and managing layouts
- Plotting and printing drawings
8. 3D Modeling
- Creating and editing 3D objects
- Working with 3D coordinates
- Applying materials and rendering
9. Customization and Automation
- Customizing the AutoCAD environment
- Creating and using macros
- Introduction to AutoLISP for automation
10. Project Work
- Applying learned skills in a comprehensive project
- Reviewing and refining project work
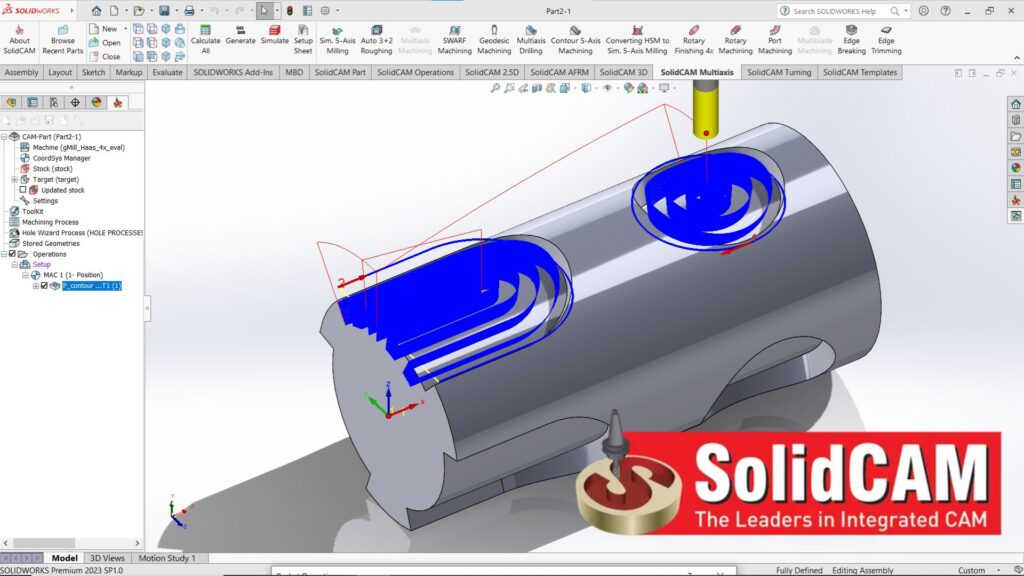
SolidCAM Course
What's in this course?
Creating a SolidCAM course would typically cover a range of topics from basic to advanced, including the following areas:
1. Overview of SolidCAM:
– What is SolidCAM?
– Benefits and applications
– Integration with SolidWorks
2. User Interface:
– Navigating the SolidCAM interface
– Customizing the workspace
– Basic tools and features
3. Setting Up a Project:
– Creating a new project
– Importing and exporting files
– Setting up units and measurements
4. 2.5D Machining:
– Introduction to 2.5D milling
– Creating and defining tools
– Basic 2.5D operations (drilling, contouring, pocketing)
– Simulating and verifying toolpaths
5. 3D Machining:
– Introduction to 3D milling
– Advanced 3D toolpaths (roughing, finishing)
– Surface machining techniques
Specialized Topics
10. iMachining:
– Introduction to iMachining technology
– Benefits of iMachining
– Setting up and optimizing iMachining toolpaths
6. Turning Operations:
– Introduction to turning
– Creating and defining turning tools
– Basic turning operations (facing, roughing, finishing)
– Simulation and verification
Advanced Operations
8. Multi-Axis Machining:
– Introduction to multi-axis machining
– Creating and defining multi-axis tools
– Simulating multi-axis toolpaths
– Advanced multi-axis strategies
7. High-Speed Machining (HSM):
– Introduction to HSM
– Strategies for efficient machining
– Toolpath optimization
9. Mill-Turn Operations:
– Introduction to mill-turn machining
– Coordinating milling and turning operations
– Simulating mill-turn processes
11. Automation and Customization:
– Using macros and scripts
– Customizing post-processors
– Automating repetitive tasks
Practical Applications
12. Project-Based Learning:
– Real-world projects and case studies
– Applying learned concepts to practical scenarios
13. Best Practices and Tips:
– Efficient workflow tips
– Troubleshooting common issues
– Maintaining and managing tools and machines
Certification and Assessment
14. Review and Assessment:
– Review of key concepts
– Hands-on assessment projects
– Preparation for SolidCAM certification exams
Resources and Further Learning
15. Additional Resources:
– Books, tutorials, and online courses
– Forums and community support
– Continuing education and advanced certifications
This content can be tailored based on the audience’s level (beginner, intermediate, advanced) and specific industry needs.